As the title would suggest, comparing human health to equipment asset health reveals some striking similarities, but also uncovers differences that should be considered. In the world of tribology and equipment lubrication, we often use the illustration that “anything a doctor can do with blood, we as maintenance and engineering professionals can do with various kinds of lubrication.” The human body is the most remarkable organism - or machine if you will - known to humankind. We proactively undergo examinations (diagnostic testing), and when the results are not what we are hoping for, we move heaven and earth to do anything we can within our power to preserve our health and save our lives.
What about high-dollar, mission-critical equipment and machines that are the heart and soul of a business organization? Do we do the same for the equipment we are entrusted with? Do we move as fast or pay the same amount of attention? What would happen if we paid more attention to that report, that dashboard alarm, and prioritized our corrective actions based upon actionable insight, information, end-user domain knowledge, common sense and a dose of good old-fashioned wisdom?
Human Health Diagnostics vs. Equipment Health Diagnostics
I am in the middle of dealing with my own health crisis because of a recent diagnosis and treatment of B-Cell Non-Hodgkin’s Follicular Lymphoma. In June 2021, I found a lump in my neck and reported it to my medical team. Once reported, this led to additional blood tests, ultrasounds, CAT scan, live X-ray needle biopsy and then a PET Scan to confirm the assumed diagnosis and next steps. None among us ever wants to hear those three dreaded words: “You have cancer!” However, being able to assess all the data available to me, examining statistical outcomes of the treatment efficacy available and getting expert advice from oncologists and other specialists allowed me to make the wisest decision that was right for me.
Compare and contrast that to the reality of asset and equipment health management. I have been involved in the business of tribology and lubrication as an end-user, reliability engineer and vendor in industries such as mining (both surface and underground), heavy construction and aggregates, rail transportation, oil and gas and renewable energy. I have seen organizations deploy state-of-the-art condition monitoring and analysis technologies in the form of inline oil sensors, wireless vibration accelerometers, SCADA data, Artificial Intelligence (AI), Machine Learning (ML), Industrial Internet of Things (IIoT), Edge Computing and Big Data - always with the thought that this would be the next all-encompassing silver bullet to solve every issue.
In the end, a piece of hardware, a sensor, an oil sample, an FFT or a thermography image is just that - a bit of data that needs to be prioritized, acted upon with root cause identification and resolved through a deliberate course of action. In the high-dollar engineering and maintenance world, professionals are required to act with deliberate and intentional purpose, or the outcome is nothing more than putting out fires, changing parts, maintaining the status quo and performing business as usual.
Technology is great. The advancements that have been made in just the last ten years alone in the field of machinery condition monitoring have been amazing. But successfully utilizing the data these tools give us really boils down to action and prioritization - moving from a diagnostic approach to a prognostic approach. This requires combining the data from technology sources with a solid understanding of and commitment to basic maintenance fundamentals and traditional oil analysis.
Your outcomes, will be different than another maintenance or reliability specialist at a different organization based on your environmental conditions, maintenance expectations and personal experience. Using your experience, gathering insights from oil analysis reports and sensor data and combining that with the expertise of your lab and lubrication vendor will help you make the wisest decision.
Three Stages of Response
What we discussed above is essentially the “stages of response” you would go through after receiving results from testing. The three stages include interpretation, decision and action. These stages can apply to both machine health monitoring and human health. Just as with my own cancer diagnosis, you need to be able to bring together all the data available, examine the options available, make the wisest decision for your equipment and organization and then act on that decision.
1. Interpretation
- Questions about the results: Do you have trust in the numbers, flags and commentary? If you do have concerns, chat with your laboratory (or doctor) to get more details.
- Knowledge of the situation: This is typically an internal conversation - you may discuss it amongst your family or dive deep into your own understanding of your situation. From an organizational perspective, your operations group should be able to provide context around oil service hours, component hours and recent repairs that can potentially impact the interpretation of the results.
- Additional perspective: Different parties can interpret results differently, so getting perspectives (or second opinions) from equipment manufacturers, oil suppliers or other sources can help build consensus.
2. Decision
- Weigh your options and make the call: You could be faced with a “do something or nothing” decision, or you may have multiple options to consider - whatever the decision, it will impact the response protocols implemented.
3. Action
Ignore the results: If you decide not to respond to the oil analysis results (or your doctor’s recommendations), carefully consider what result would require an immediate response and include them in your protocols.
- Gather more perspective: Like gathering perspectives within the Interpretation phase, you can gather more perspective on how to respond from the OEM or oil suppliers (or peer groups and other medical professionals) and decide the best course of action.
- Monitor more closely: Depending on the results, you may determine that you need to stay the course but monitor the situation for a period of time. For equipment health, more frequent oil sampling, additional testing or cross comparison against other condition monitoring techniques (e.g., vibration) may be in order. Again, set the protocols for what additional monitoring should be done and the timing and triggers for immediate response.
- Perform an inspection: Depending on the issue’s severity, humans will get additional tests and biopsies done to confirm the results and determine possible next steps. Based on the results and interpretation of your oil analysis results, you can brief your team before performing a machine inspection to help them pinpoint what to look for. Perform the repair: Sometimes, the best response is to perform the surgery or take the medication to repair the issue, followed by close monitoring. For machinery, the most common initial repair response is to change the oil. Follow-up with additional monitoring (e.g., oil sampling, condition monitoring) to confirm if the issue is resolved or if further action is required (e.g., inspection).
- Change the PM interval: Shorten or extend the PM interval to determine if the oil analysis results improve or degrade. This is similar to shortening the time between doctor visits and testing in order to monitor an improvement or decline in health.
- Improvement projects: If you see a recurring problem happening, consider additional improvement projects to resolve the issue, such as flagging optimization, training and process mapping. For your own health, this could mean diet, exercise and changes to your overall lifestyle.
Objectives for Consideration
As simple as it may seem (get the data, interpret the data and decide), when it comes to setting out on a course of action for equipment maintenance (or human health maintenance, for that matter), one also needs to consider the following:
-
You run a marathon of 26 miles, 385 yards and 10 feet. If you know the goal but forget to watch for the holes in the road, the rocks, the uneven surface or the first hill at mile one, it could mean the difference between finishing the race or losing focus and getting injured. A marathon is not a sprint; it is a long, hard race, not for the faint of heart. Neither is it easy to change the course of a less than effective maintenance program. Live with a mindset of continuous improvement, making incremental changes each day. -
Keep the main thing the main thing
Do not let individual or chronic problems continue to go south. Knowledge is power, and sometimes things can be explained and corrected. We are all human beings and have vain imaginations. Do not become polarized by data or overanalyze it (analysis paralysis). Be cautious, not paranoid (there is a significant difference). As a leader, you set the vision of where you are going and what the future looks like. You then set the mission as to how your team gets there (responsibilities and action plans). -
Correct course as soon as possible
From time to time, you may need to course correct because of internal or external issues. It is important to get back on course as fast as you can to limit the possible downstream effects if your response is too delayed. Set up realistic goals and key performance measurements; as the saying goes, “that which gets measured gets done. -
You have a team to support you
Reach out and ask for help. You do not need to carry the weight of this alone. We do not always need to be the smartest person in the room and as you look around your team, empower them; let them have a part in the learning and the success that will come. I have always believed that the answers will be found in the room. Lean on your team and trust them to do their jobs. -
The answers are indeed in the room
Empower your team to speak their minds if they have a better or innovative solution to an issue. Anything less than that is a disservice to one another, to your organization and to the voiceless equipment you are charged with managing. I know that I expect - no, I demand - that kind of thinking and leadership from my oncology team. Wouldn’t you? -
Take bad thoughts captive
Do not let your bad thoughts live rent-free in your head. By this, I mean we tend to worry about things that never happen. We worry about things we do not have control over - things that happen regardless if we worry or not. Lastly, we worry about things from yesterday or tomorrow, and because both of those are days we do not have, we only make today worse and counterproductive. Put your energy into things you have direct control and influence over. Be aware of the other things and learn from them but have a short memory (that includes the good and the bad). Tomorrow is a day found only on a fool’s calendar. -
You are in charge of the data
Not the other way around. All these things are tools - arrows in your quiver; use them wisely, but do not be a victim of analysis paralysis. Think of this as using the proper wrench size and type (metric or SAE) for the proper application. Do not be a victim. If you have an oil analysis program that triggers water at too low of a ppm and you have zero capability of achieving that, then make relevant and applicable adjustments. The same would go for ISO Particle Count Cleanliness and other test flags. If you do not take charge of your data, all you have is white noise or a dashboard of yellow and red alerts that are demoralizing, and your team will lose focus. -
If not me, then who?
Our world is always looking for somebody else to do the job and take the blame, so inevitably it gets overlooked. If you see a need, take charge. You do not have to be the leader to be in charge; leadership is about influence. It is all about super accountability and if everyone could apply just a bit of that, think of what our improvements could be. -
Anything worth doing is worth doing well
Our world is full of mediocrity, so do not strive to be the second best. Stop for a moment and think of all the Olympic Medal Winners, from Gold to Silver to Bronze and even those that might miss the medal platform altogether. In many cases, only tenths of seconds separate first from fourth and beyond. Strive to be the best as humanly possible within your capabilities. In the end, all we are responsible for is our attitude and our efforts. -
When faced with unwelcome news, press in
Everything is not about you but should be about others. When life throws you a curve ball, swing for the fence. Be a blessing to others on your team. Do not be a complainer but rather a solution provider. A bad attitude is truly just like a cancer: it seeks to eat, destroy and devour all that is good. Life owes none of us anything but a chance and what we do with that chance is completely up to us.In a comparable manner, think of how you can apply this philosophy to your job as a maintenance or engineering professional. You speak on behalf of your equipment - your assets that do not have a voice and cannot speak on their own behalf. Every day, week, month and year, countless components will fail (with many failures being lubricant-related). Having a vigilant, well-informed oil analysis program is one of the best steps to take. My father used to say to me, “Do not be a dumb smart guy; do not let your fancy schooling and book learning get in the way of your real education and learning when you are in the field working with old Bessie - the engine, pump and hydraulic system. If you listen closely to her, she will tell you what is happening, what is ailing her.
Conclusion
I have many challenges before me with my health, and if anything, this has taught me to value what is important: to love people and to always be willing to pass along what I know to make our world a better place. Employing a state of urgency causes self-reflection in establishing my personal and professional priorities, such as what I do today and what really counts from an eternal perspective. I look at what impact I have on the lives of those I work with, being a servant leader and leaving a legacy when I have taken my last breath.
At present, my prognosis has been a “watch-and-wait,” meaning that just like a maintenance professional, I will take more frequent “oil” samples and then do triggered testing based on those results. I will closely watch the trends, react accordingly, and do my absolute best to take care of myself with rest, nutrients, exercise and ensure a healthy work-life balance. When we have our health, we have everything and should pattern or copy this approach to some extent into our professional lives. Our equipment will run itself to destruction if we let it. It is not sentient and depends on you to be its advocate.
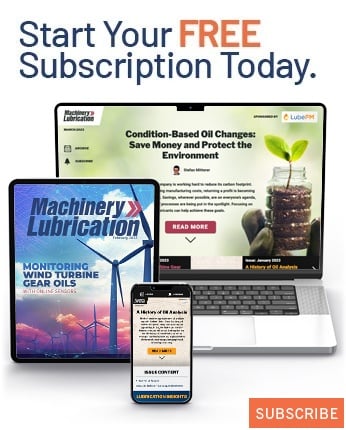